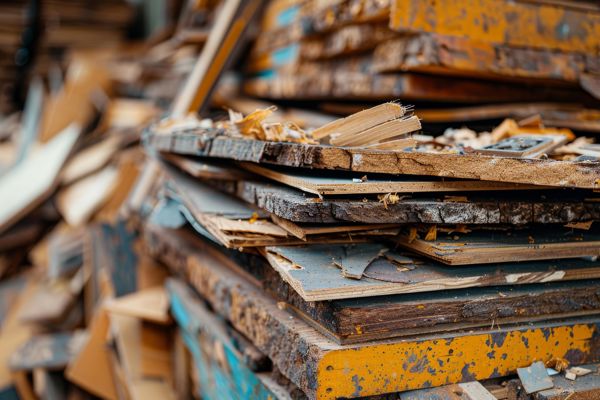
Extended lifetime for kitchens
Value chain collaboration under Closing Loops
Value chain collaboration under Closing Loops
The lifetime of kitchens is expected to be extended from the current 11.4 years to 30 years, so that resources are better utilised.
Replaced doors etc. are sent to Kronospan to be reused. More building projects are seeking solutions where their excess timber can be used in new products, and this is possible at Kronospan.
Collaborative work is being done in the value chain together with other value chains to utilise textile waste to replace wood fibre in chip boards. The criteria for use are the same as for wood fibre: It must be recyclable 7-8 times.
The project’s businesses develop solutions that extend the life cycle of kitchens, which can bring about new business opportunities and reduce environmental pollution. By focusing on re-use and repair, the participating businesses can differentiate themselves in the market with sustainable products that appeal to environmentally-conscious consumers. The project gives access to collaboration and knowledge sharing with other actors, which could inspire innovative initiatives and strengthen the participants as forward-thinking, responsible businesses in a competitive market.
Design for disassembly:
Already in the design phase, develop materials and constructions that can be recycled after end of life cycle. Chip boards can be reused, but edging strips, laminates, handles and fittings sometimes can not. It must be possible to separate everything in order to recycle.
Construction:
Develop new kinds of constructions and fittings that make it possible/easier to replace worn out or broken parts without replacing entire elements or kitchens.
Re-do:
Conceptualise the replacement of e.g. cupboard doors and kitchen surfaces instead of complete kitchens to ensure a new look and replace worn parts instead of the entire kitchen. Ensure effective business processes (measurement, order processing, production, logistics and fitting), so that the concept is economically attractive for customers, sellers and manufacturers.
Recycling:
In Denmark we have a well-functioning system where used kitchens are delivered to recycling centres, from which wood and chip boards are returned to chip board manufacturers. Here, the elements are crushed, and the material is reused. The challenge is: everything is crushed, regardless of whether some of it could be re-used. Could we perhaps develop a recycling system for used kitchens aimed at re-use, repair and repainting?
The project will develop and implement quality assurance methods that lead to high quality products with high durability over a long life cycle – despite using recycled materials. Prototypes will be produced and demonstrated, and new or improved products or production methods will be tested and validated in pilot projects.
“The lifespan of kitchens must be extended to optimise resource use. Collaboration across value chains creates new, innovative solutions.”
Value chains span across industries, and studies show that collaboration fosters circular implementation and enhances competitiveness.
This project is part of Closing Loops, a close-knit community of small and medium-sized Danish enterprises that, together with skilled experts, develop concrete circular solutions within value chains.
The goal is to explore new ways of collaborating across industries and geographies, leading to both transformation and business opportunities.
Participating companies gain a significant and essential circular boost by working to minimise resource consumption and waste. They also implement solutions that unlock new development and business opportunities.
The project is part of Closing Loops closingloops.dk.
The kitchen design market in Denmark is one of the largest users of chip boards. There is a need to extend the life cycle of kitchens and to utilise excess materials from old kitchens.
Today, it is possible to produce chip board using up to 100% of recycled wood. Chip board is recyclable 6-7 times. There is a need for waste wood to be better utilised as a resource, e.g. as chip board, instead of burning it.
Kronospan, a manufacturer of chip board, currently lacks waste wood materials and is focused on ensuring supplies through improved collaboration with recycling centres in Denmark. They are collaborating with the value chain via take-back schemes and with businesses that have large quantities of waste wood which currently is sent for incineration.
Group delivers 25-30 thousand kitchens a year and operates with take-back schemes and repair of old kitchens.
Kronospan is experimenting with improved material flows from used wood and textile fibres in chip boards. They are working on tracing their re-used chip boards from old kitchens in order to measure the recycling and life cycle.
&Shuffle has experience from concepts for upgrading IKEA kitchens, which is used in the project to kick start a larger-scale set up with higher volume.
Stykka designs and produces products for circular building and furniture. Their experience is used to develop solutions that extend the life cycle of kitchens.
AFLD helps with input to improve the recycling of waste wood and old kitchen elements.
Så er der to muligheder: